项目简介
数字化工厂(DF)是指以产品全生命周期的相关数据为基础,在计算机虚拟环境中,对整个生产过程进行仿真、评估和优化,并进一步扩展到整个产品生命周期的新型生产组织方式。现代数字制造技术与计算机仿真技术相结合的产物,它的出现给基础制造业注入了新的活力,主要作为沟通产品设计和产品制造之间的桥梁。各大城市都有智能工厂的规划,本项目针对传统工厂数字化转型,提供智能工厂建设的解决方案。
技术优势
1、将现有设施生产力提高15%-20%;
2、将规划新生产设施的投资减少20%
3、减少库存和生产时间达20-60%
4、优化系统大小,包括缓冲大小
5、更早验证设想,减少投资风险
6、更大程度地利用生产资源
7、改善生产线设计和进度表
应用场景
(1)虚拟设计:在项目实施之前依据设计、装备、工艺等数据模型,对产品未来的制造、乃至全生命周期的过程进行虚拟仿真,达成对未来生产过程的预测、评价、工艺、时序、交期、成本、能耗及人工等进行精准的分析与改进,并完成产线布局及信息化模拟,在项目实施之前即对方案做出最优化的决策。
(2)辅助决策优化:项目投产之后将实际生产过程的大数据导入虚拟仿真系统,通过优化的控制方案及经验累积,不断地加快研发进度、提升产品质量及生产效率、降低生产成本及能耗、增强企业管理决策与生产控制水平。
(3)系统展示:实际制造过程中虚拟仿真系统通过与实际工厂生产过程数据的交互,可展示产品制造流程的全方位、多角度、无限接近真实工况的各项信息,以展现生产过程的透明度、提升对企业先进制造能力的可信度。
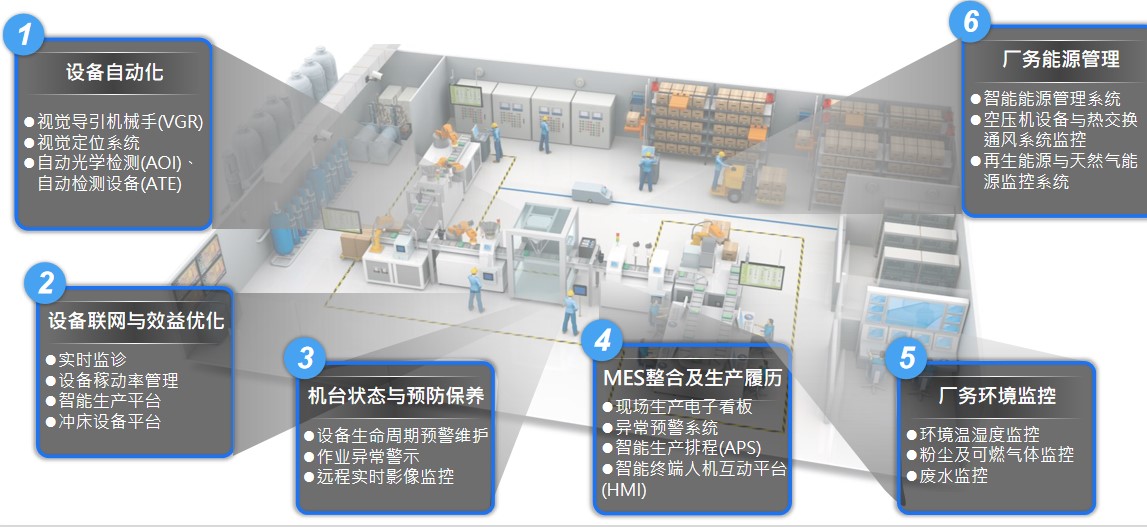
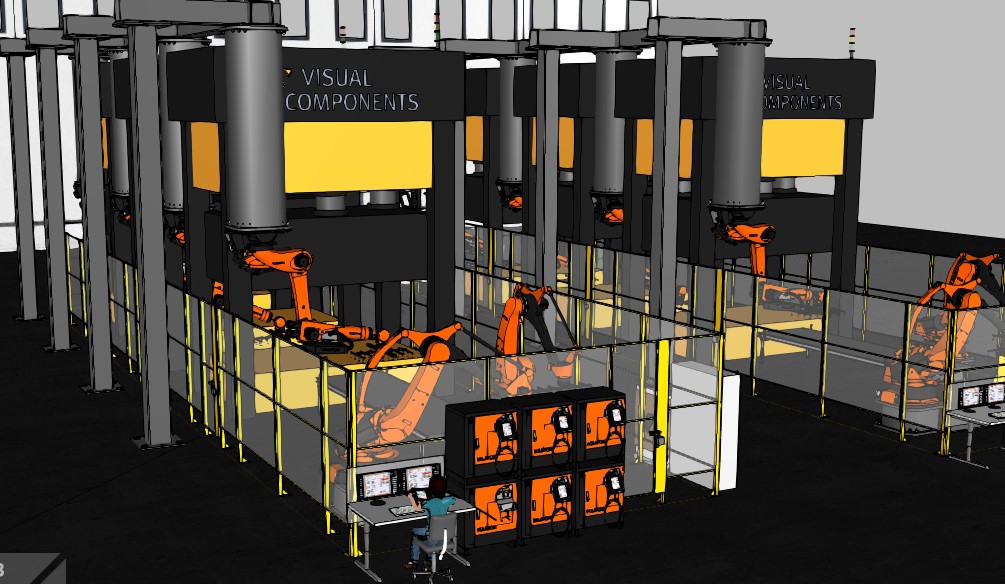
应用案例
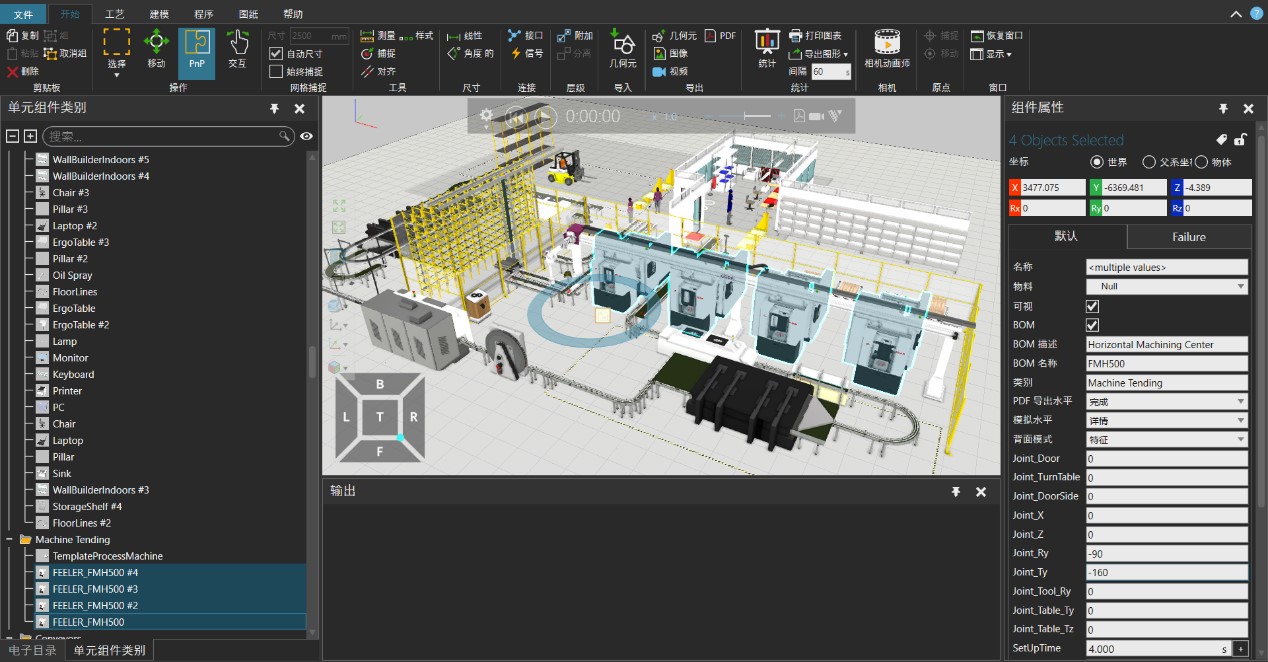
大型滚珠轴承的生产线。通过二次开发实现设备利用率的实时交互显示,通过调整物流路径、生产节拍,设置缓冲区,制订了3种优化方案,优化后生产能力从每月度50件,提升到每月226件,产能提升3倍,创造价值千万余元。
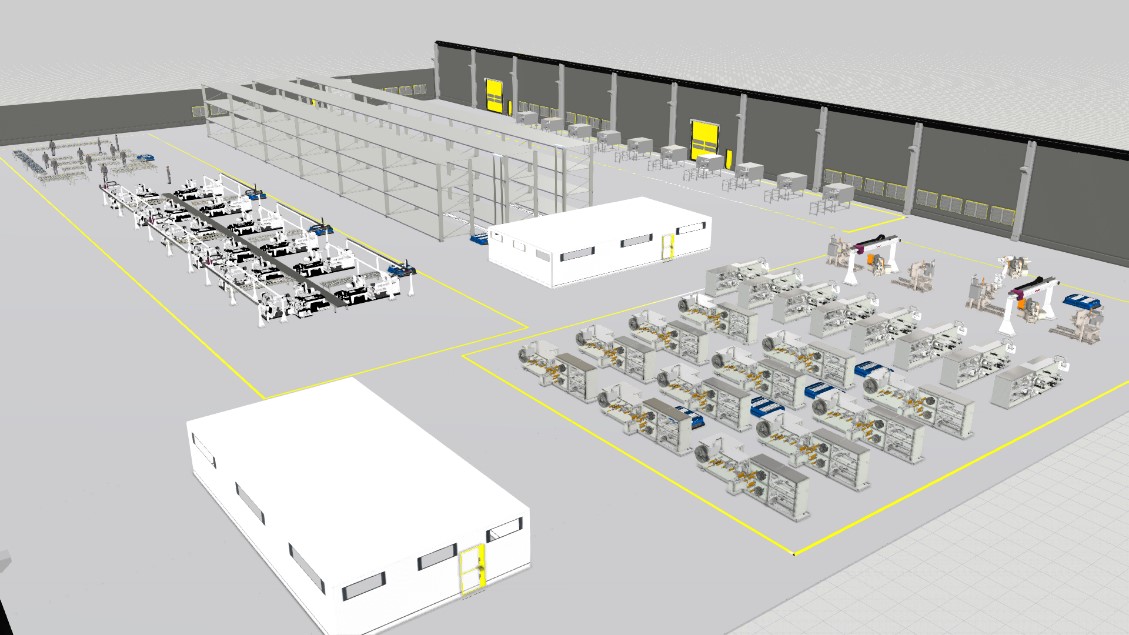
非晶立体卷生产线。实现了全流程的生产可视化,并在建厂前进行产能预测及节拍仿真优化,降低了产线试错成本。根据生产实时推送各工序加工、物流指令与现场采集装置数据交互获取必要的实时信息,并将仿真信息推送至各智能终端。达成了少人干预生产,设备预测性维护的目标。